-1.png?width=300&height=58&name=CONFORMiT_Logo_Green%20%20(6)-1.png)
BETTER LOTO CAN
GENERATE MILLIONS
Is the handoff from production to maintenance actually losing your mill money?
Is the handoff from production to maintenance losing your mill money?
5 minutes = $500,000
Every hour, the average mill produces $16K worth of product. Losing even 5 minutes due to inefficient communications (between production, maintenance, and operations) or confusion around ECPs equals a loss of $1300 per lockout. Calculate that annually and you’re looking at roughly $500 000 in lost production.
Implementing CONFORMiT Lockout Tagout Software drastically reduces equipment downtime. Creating even a single minute of uptime every day, on one machine, adds $100k of additional production in a year.
Tightening up the gap between production and maintenance isn’t rocket science, but it does require accurate synchronization and careful planning.
IMAGINE AN F1 PIT CREW
Tools are already spinning and people are already on the move before the car even stops, in order to make sure that they execute the fix as quickly as possible - minimizing time spent off the track.
4 SIMPLE STEPS TO SUCCESS
1. MEASURE YOUR CURRENT PROCESSES
How often do you experience flatline gaps? How much time does each step take? Who’s really involved and when exactly are they involved? You can even dig a little deeper and identify competing responsibilities that prevent workers from accomplishing their mission critical task. Book a time with Matt if you would like help to assess your current reality.
Remove false calculations and common assumptions around how your facility operates. In turn, build a team that is aligned and focused on a common goal.
2. IDENTIFY BOTTLENECKS
Examine where your bottlenecks are. When and where do things slow down? What elements are then delayed in consequence.
Identifying and indexing all of the problems in your mill is beyond overwhelming. Prioritizing your bottlenecks will guarantee the quickest, most impactful changes.
3. CALCULATE POTENTIAL
Take the data from your bottlenecks and calculate the potential throughput increase that fixing this step would generate. Is it significant? How much additional uptime will you gain? Would implementing the fix have a negative affect on an other area of the process?
When data speaks, everybody listens. Calculating your potential is the shortest path to genuine optimization.
4. HOST A ROUNDTABLE
Once you’ve gathered all your information, it’s time to call in the stakeholders. There is no magic fix - it takes time, consideration, and action.
Your team is your most valuable asset. Get them onboard and plan your way to operational success together.
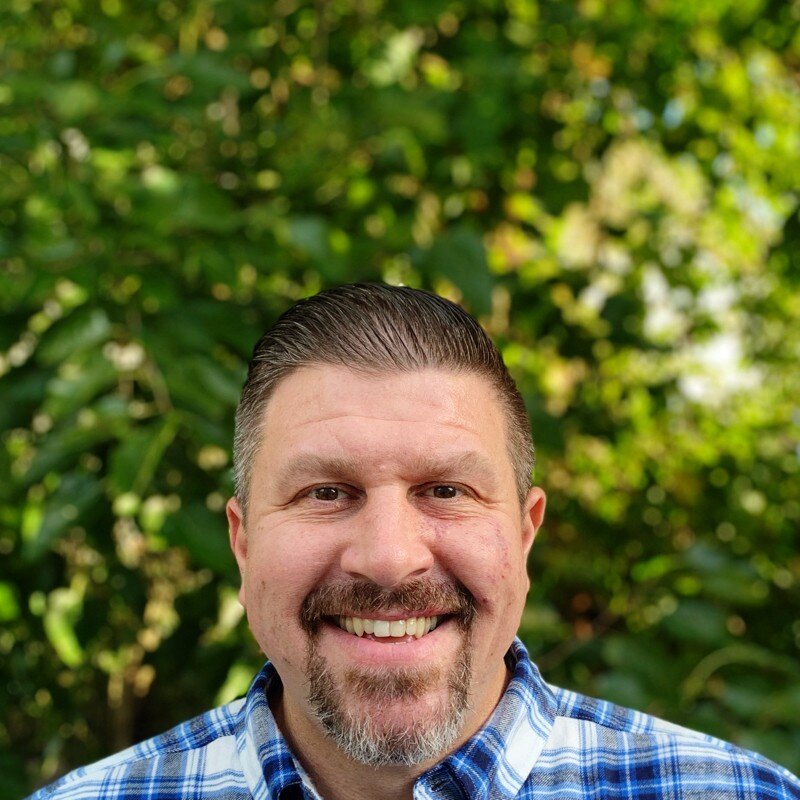
ABOUT Matthew Gleeson
HEY! I'M MATT,
I've spent the last decade decoding what solutions really mean for the buyers. CONFORMiT solutions go beyond your basic need and unlock safety excellence!
As a VP of Sales at CONFORMiT, I play a pivotal role in driving our mission forward by expanding our client base within the United States. My primary objective is to engage with potential customers in the Pulp & Paper Industry, understand their unique challenges, and offer solutions that leverage CONFORMiT's Lockout Tagout Software to mitigate risk and improve operational performance. Not to mention that the CONFORMiT way of Lockout can significantly boost your production revenue!
MEASURE YOUR CURRENT PROCESSES | How often do you experience flatline gaps? How much time does each step take? Who’s really involved and when exactly are they involved? You can even dig a little deeper and identify competing responsibilities that prevent workers from accomplishing their mission critical task.
IDENTIFY BOTTLENECKS | Examine where your bottlenecks are. When and where do things slow down? What elements are then delayed in consequence.
CALCULATE POTENTIAL | Take the data from your bottlenecks and calculate the potential throughput increase that fixing this step would generate. Is it significant? How much additional uptime will you gain? Would implementing the fix have a negative affect on an other area of the process?
HOST A ROUNDTABLE | Once you’ve gathered all your information, it’s time to call in the stakeholders. There is no magic fix - it takes time, consideration, and action.
